Since 1968, weโve specialised in precision chemical etching of metals, earning a global reputation for excellence with outstanding customer service, fast lead times, and top-quality management.
We offer value-added services our customers trust to meet the highest standards.
With decades of experience, we ensure every project meets the highest quality. Our reliable, advanced processes have earned us a bronze SC21 accreditation and a 98% on-time delivery rate. We operate to rigorous standards, including SC21, ISO 9001, 14001, and 45001, ensuring full traceability. Combining industry expertise, state-of-the-art equipment, and a trusted partner network, we deliver precision manufacturing solutions tailored to your needs.
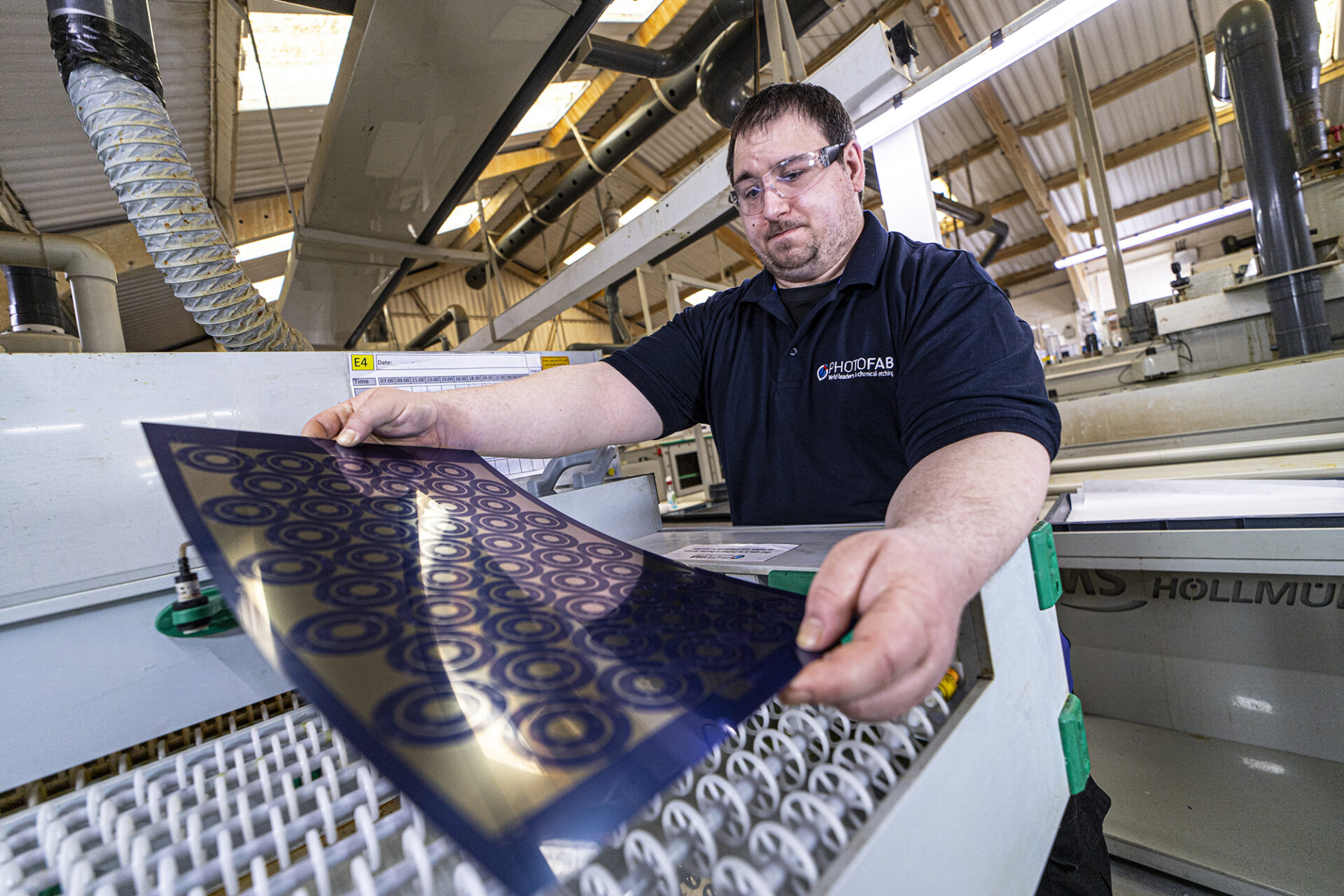
What is chemical etching and how does chemical metal etching work?
Chemical etching is a highly precise and versatile manufacturing process used to create intricate, detailed components. By using acids and other chemicals to dissolve specific areas of a metal sheet, this method achieves levels of accuracy and complexity that traditional machining techniques often cannot match.
The process removes as little as 10 microns (0.0004โ) and up to over 0.5mm (0.020โ) from both sides of a metal sheet simultaneously, making it an efficient and highly controlled technique. The result is a component with finely etched details and exceptional dimensional accuracy. For further insights, explore our detailed metal etching process section.
It is compatible with a wide range of metals, including brass, copper, beryllium copper, and ferrous materials like stainless steel, carbon steel, and mild steel, with thicknesses up to 1.5mm.
For metal cutting needs that exceed 1.5mm thickness, up to 22mm, we can also offer laser cutting whilst ensuring the same high standards of precision and reliability. Whether you require chemical etching or laser cutting, our expertise ensures your components are manufactured to the highest quality, customised to meet your exact design specifications.
Behind the chemical etching process
Chemical etching is celebrated for its flexibility and precision, making it an ideal choice for a variety of industries. From electronics and aerospace to medical devices and automotive parts, this process is used to manufacture components that require intricate designs and tight tolerances.
Hereโs a snapshot of our photo chemical milling (PCM) process
1. Design Advice
Collaborate with our engineers to refine your design, reduce costs, and ensure manufacturability through CAD files or a simple sketch.
2. Receipt of Drawings
We digitise your drawings into CAD and optimise them for material usage, adapting for etching accuracy.
3. Film Plotting
Laser-plotted graphic tools ensure component precision from both sides of the metal.
4. Metal Selection
Choose from our vast metal stock available with full traceability and certification.
5. Metal Preparation
We cleanse every metal sheet, ensuring itโs free of impurities for seamless image transfer.
6. Resist Lamination
Double-sided photosensitive polymer films coat the metal to enable the precise transfer of designs.
7. Printing
Your design comes to life as the coated metal is UV-exposed with your graphic tool for intricate detailing.
8. Developing
The unprotected areas of the resist are chemically developed away, readying them for etching.
9. Etching
Bespoke chemicals then remove exposed metal, creating dimensional perfection.
10. Stripping
This is the final process The resist is stripped from the final design, revealing clean, flawless metal components.
11. Inspection and Packing
Every component undergoes rigorous testing to ensure accuracy, quality, and surface integrity before being securely packaged for delivery.
Etching Tolerances
chemical etching services
For prototyping
Prototyping is often a painstaking process of trial and error โ even minuscule design changes can cost valuable time and money. Chemical etching drastically reduces the cost and time consumption of these experiments. Rapid prototyping is possible, ensuring that you can easily implement cost-effective improvements. See our Rapid Turnaround Service for more details.
Chemical etching bridges the gap between prototyping and full production, using the same tooling to make one part or a million. Weโd be happy to discuss how we can bring your ideas to life, so you can see a return on your hard work. Send us your specification to get a quote within 24 hours.
For Volume Production
Continuous investment into the business and the team has delivered the latest advancements in automation technology and processes. Every stage in production has been refined to offer the highest standards with the shortest lead-times possible, from digital tooling, with quick and easy changes to specifications, multi-component designs all on one sheet, through to our multi-sided burr-free metal etching and automated stripping line.
The entire process from quote to delivery has a dedicated point of contact, reinforcing the production process, with full traceability throughout.
Our Chemical etching tabbing GUIDELINES
In order to further increase the precision of components, we โtabโ parts into sheets of metal. Tabs are slivers of metal, that serve to retain parts in sheet form. In other words, once completely etched, the components are not โlooseโ parts, but instead are held into sheet form using these tabs.
We have devised four different tab styles. These are shown below along with features of each.
Inboard Twist Tabs
- Full thickness twist tab
- Leaves minimal material loss and no protrusion
Half etch outboard tabs
- Used when small protruding witness is acceptable, or when inboard is not an option
- Can be finished on thicker materials to remove protruding witness
Half etch inboard tabs
- Half etched break line style
- Used when a small protruding witness is not acceptable
- Breaks slightly inboard or on the component edge leaving no protrusion
Full thickness outboard tabs
- Used when small protruding witness is acceptable โ or when inboard is not an option
- Can be finished on thicker materials to remove protruding witness
*1mm is not the dimension of the feature, but is for scale reference only
Tab-less parts can be made if required.
The essential guide to getting the most from our Versa-Etch Technology
Reduce costs and optimise prototypes with our Versa-Etch technology.
Our guide details how this flexible chemical etching process allows for cost-effective multiple designs on a single sheet.
FAQs about chemical etching
What metals can be etched?
We can etch a wide selection of metal alloys including stainless steel, aluminium and copper. There are a couple of metals that we canโt etch including tungsten and titanium..
How accurate is the chemical etching process?
Our chemical etching process supports extremely tight tolerances, ensuring flawless results consistently. The tolerances differ based on the thickness of the metal and they can be dimensional, positional, etching and thickness tolerances. Please see the graph above for more information
Can you handle custom designs?
Absolutely, we pride ourselves on creating highly bespoke parts and components. We can work with a fully dimensioned CAD file to a simple description. Our team will work with you to bring your unique ideas to life.
Will the process alter the metal properties?
Not at all. Chemical etching uses no heat or force, ensuring the materialโs properties remain unchanged. We can offer additional processes such as heat treatment, annealing or anodising upon request.
What are the benefits of chemical etching?
Low-cost tooling
Low-cost design changes
Mixed graphic tools for prototyping to full production runs
Half-etched forming
Metal properties remain unaltered
Can I add identification marks to my parts?
Yes, you can easily add company logos, part numbers, or other identifying marks to your parts during the chemical etching process.
Value added partnerships
We also have long working relationships with specialist partners for additional finishing services. These services can range from laser-cutting, plating, anodising and heat treatments which can add decorative finishes, prevent corrosion, and further improve durability.
All additional processes are managed closely and delivered with full transparency and traceability.
start your production journey today
If you are looking to find a complete service include dedicated engineering to design and implement your solution, get in touch with us. Youโll be given an account manager who is always on hand to advise and take care of everything for you. Call us on 01480 226699 or contact us now to see how we can add an extra dimension to your manufacturing project.
TAKE A LOOK AT OTHER
SERVICES we offer
To find out how we can help you